Table of Contents
ToggleWhat is a transformer winding
The transformer winding is the key part of the device through which the electric current flows, creating the magnetic field necessary for energy transformation. It consists of many turns, which can be made of copper or aluminum wire. The winding is the main element through which energy is transferred from one coil to another, creating an electrical voltage in the corresponding circuit. A transformer can have several windings: primary (input) and secondary (output), which are located on the magnetic core. Thanks to the winding, the required voltage and current changes necessary for the efficient functioning of electrical systems are achieved.
Transformer winding design
Transformer winding design involves several important aspects such as conductor arrangement, number of turns, laying method and insulation type. The first step is to select the conductor, which can be round or flat, depending on the transformer design. The winding should be designed to maximize cooling, stability and reliability.
Basic winding characteristics:
- Number of turns: determines the voltage to be induced in the winding.
- Conductor Type: can be copper or aluminum, which affects conductivity and cost.
- Winding method: The winding can be wound in several layers or single layers, depending on the type of transformer and its capacity.
- Insulation: is used to prevent short circuits between coils and to ensure safety.
The transformer winding must also be designed to minimize energy losses and optimize cooling processes. It is important to consider the mechanical strength of the materials so that they can withstand various loads and prevent damage during operation of the device.
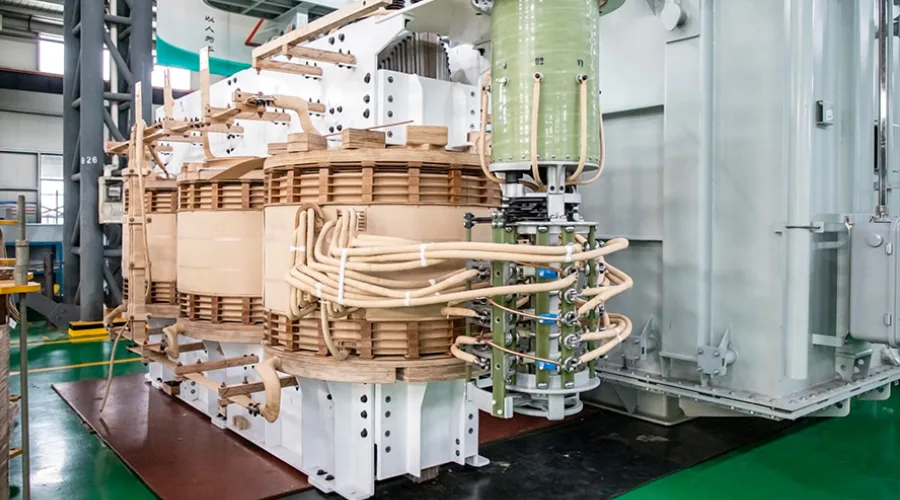
Classification of transformer windings
There are several types of windings that are categorized based on design and purpose:
Cylindrical single and multilayer winding
- Benefits: Easy to manufacture and good heat dissipation.
- Disadvantages: Low mechanical strength.
Cylindrical multilayer winding with flat wire
- Benefits: Easy in production process, good fillability of the magnetic core.
- Disadvantages: Reduced heat dissipation area compared to windings with radial cooling channels.
Multilayer cylindrical winding with round wire
- Benefits: Ease of production.
- Disadvantages: Mechanical strength deteriorates with increasing power, heat transfer properties are reduced.
Flat wire windings (two-wire and multi-wire)
- Benefits: High mechanical strength, good cooling and reliable insulation.
- Disadvantages: Higher cost compared to cylindrical windings.
Continuous winding with flat wire
- Benefits: High mechanical and electrical strength, good heat transfer.
- Disadvantages: Requires readjustment when winding half a spool.
Windings with aluminum foil
- Benefits: Good magnet core fillability, high mechanical strength.
- Disadvantages: Complex manufacturing process for high voltage windings.
Thus, the choice of winding type depends on many factors, including transformer power requirements, type of cooling, intended use, and cost.
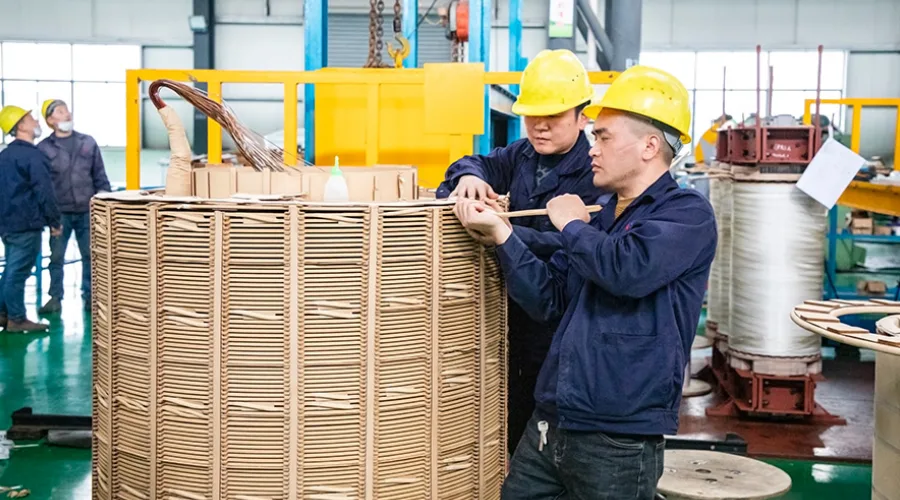
Different types of transformers and their windings in Russia
Depending on the purpose and application, transformers can use different winding designs that are optimized for specific operating conditions. Various types of transformers are manufactured in Russia, each with unique winding requirements depending on their purpose, power and voltage class. Let's take a look at several types of transformers and their corresponding windings:
1. Power transformers (low, medium and high voltage)
Power transformers are widely used in power systems to convert high voltage to low voltage and vice versa. These transformers are characterized by windings that can be made with either flat conductors or round conductors, depending on the type of transformer.
Windings for power transformers: multilayer cylindrical windings with flat wire or round wire. They must have good heat exchange properties, high mechanical strength and reliable insulation.
Capacities and voltagesFrom 10 kVA to 500 MVA, with operating voltages from 6 kV to 220 kV.
2. Distribution transformers
Distribution transformers are used to transmit and distribute electricity within industrial and residential complexes. These devices generally operate at lower voltages and have a lower capacity than power transformers.
Windings for distribution transformers: single and multi-layer cylindrical windings with flat wire. These transformers also utilize flat windings with straight conductors, which help to cool the unit efficiently.
Capacities and voltagesFrom 10 to 1600 kVA, with operating voltages from 6 (10) kV to 35 kV.
3. Transformers for railroads (railroad transformers)
Railway transformers are essential for powering railway lines and substations. They must be highly reliable and resistant to external influences.
Windings for railway transformers: as a rule, multilayer windings with flat wires and a high level of mechanical strength are used, as they operate under extreme conditions.
Capacities and voltagesFrom 25 kVA to 1000 kVA, with operating voltages up to 35 kV.
4. Transformers for special applications (e.g. solar and fish projects)
These transformers are used in specific projects such as solar power plants and projects to integrate solar panels with aquaculture (e.g. for sustainable electricity supply).
Windings for specialized transformers: can be made using multilayer cylindrical windings with aluminum foil to improve heat transfer and mechanical strength.
Capacities and voltages: vary depending on the application and can range from 10 kVA to 5000 kVA, with operating voltages from 6 kV to 220 kV.
5. Transformers for high voltage lines and substations
High-voltage transformersThe windings used to transmit and distribute electrical power over long distances require a very precise and reliable winding design to operate at high voltages.
Windings for high voltage transformers: cylindrical multilayer windings with foiling, which provide good filling of the magnetic core and increased mechanical strength.
Capacities and voltagesfrom 100 kVA to 5000 kVA, with operating voltages from 110 kV to 220 kV.
Conclusion
Many different types of transformers are used in Russia, each requiring a specific winding design depending on the operating conditions and purpose. The windings used can be made with different conductors, such as copper and aluminum wires, and can be made in single or multilayer configurations. It is also important to consider the mechanical and electrical properties of the windings to ensure the reliability and durability of the transformer under various conditions.